Common Challenges in Welding Inspection Madison and How to Overcome Them
Common Challenges in Welding Inspection Madison and How to Overcome Them
Blog Article
Recognizing the Basics of Welding Assessment to Make Certain Top Quality and Safety And Security
In the realm of modern-day design, welding examination stands as a keystone for ensuring both the high quality and safety of architectural productions. The procedure involves a meticulous evaluation of bonded joints, employing innovative strategies such as radiographic and ultrasonic testing to detect surprise flaws. The know-how of licensed inspectors is critical, as they connect the gap in between theoretical standards and sensible application. Their function extends past simple discovery, including the documents and interaction of searchings for to relevant stakeholders. What are the subtleties of these evaluation approaches that make them essential for keeping structural honesty?
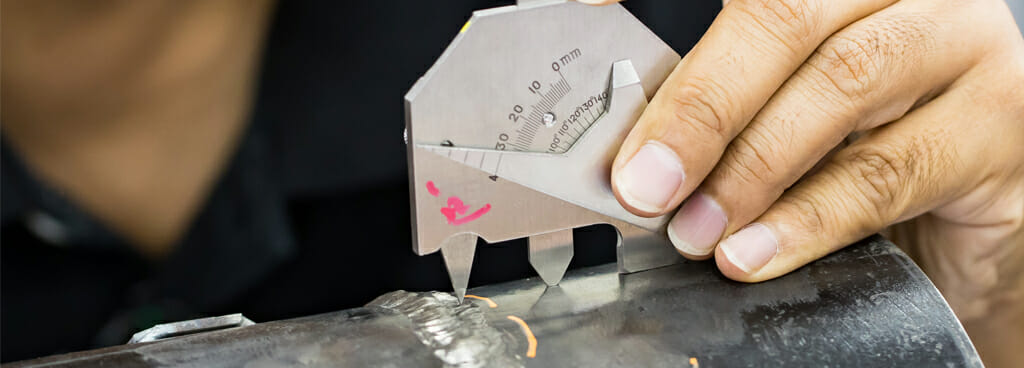
Relevance of Welding Inspection
In the realm of commercial manufacture, the relevance of welding inspection can not be overstated. Welding evaluation plays an important duty in ensuring the integrity, safety, and longevity of welded structures. Provided the diverse applications of welding in markets such as building, vehicle, aerospace, and shipbuilding, the demand for rigorous quality control steps is vital. Correct examination ensures that welds meet specified codes and requirements, which is vital for stopping architectural failings that can bring about tragic effects.
The procedure of welding naturally entails complicated variables, including temperature level, product buildings, and environmental conditions, every one of which can influence the top quality of the weld. A complete evaluation identifies issues such as fractures, porosity, and incomplete blend, which can jeopardize the toughness and integrity of the weld. By discovering these issues early, rehabilitative actions can be taken, therefore minimizing the risk of failure and linked prices.
Additionally, welding evaluation adds to regulative conformity, as lots of sectors are regulated by strict safety and security standards and standards. Failure to abide by these regulations can lead to lawful liabilities and economic penalties. Inevitably, welding evaluation not just safeguards physical frameworks but likewise shields human lives and upholds sector credibilities.

Secret Welding Assessment Approaches
Although welding inspection is vital to making certain the top quality and safety and security of welded structures, it is the specific methods utilized that identify the efficiency of the assessment procedure. Secret welding assessment approaches can be generally classified right into non-destructive screening (NDT) and harmful screening. Non-destructive screening approaches such as aesthetic examination, ultrasonic screening, radiographic screening, magnetic fragment screening, and liquid penetrant testing are mainly utilized to assess the properties of a weld without creating damages. Aesthetic assessment is commonly the very first action, including an extensive evaluation of the weld's surface for defects like splits or porosity.
Radiographic and ultrasonic screening are advanced techniques that permit examiners to assess the inner honesty of the weld. Ultrasonic testing uses high-frequency sound waves to detect stoppages, while radiographic testing uses X-rays or gamma rays to create a photo of the weld's inside. Magnetic particle screening and liquid penetrant screening are surface examination methods made use of to locate surface area and near-surface defects. On the other hand, damaging screening techniques entail physically damaging or cutting the weld to analyze its mechanical buildings. These detailed evaluation approaches make sure that welds satisfy market criteria and security requirements, therefore guaranteeing architectural integrity and efficiency.
Role of Certified Inspectors
Licensed examiners play an essential function in the welding assessment process, ensuring that all welds comply with stringent industry standards and safety regulations. Their know-how is crucial in recognizing issues or abnormalities that might endanger the architectural stability of a weld. By carefully analyzing each weld, certified original site inspectors aid protect against possible failings that might result in unsafe mishaps or expensive repair services.
To end up being licensed, inspectors must undertake strenuous training and testing, which familiarizes them with various welding strategies, products, and screening methods. This comprehensive expertise permits them to assess weld high quality successfully and make notified judgments about their safety and reliability. In addition, qualified assessors are proficient in analyzing specifications and blueprints, ensuring that the welding work straightens with the job's design requirements.
An essential part of their function is to document their findings completely, offering a thorough record of the inspection procedure. This documentation is important for traceability and accountability, functioning as a main record of conformity with industry requirements. Certified examiners additionally play a crucial role in promoting communication between task stakeholders, offering recommendations and understandings to boost welding practices and results. Their payment is essential in preserving high degrees of quality and security in welding procedures.

Devices Made Use Of in Welding Examination
Welding assessors depend on a selection of specialized devices to do their tasks successfully, making sure each weld satisfies the required standards. Amongst these devices, aesthetic evaluation aids like multiplying glasses and mirrors are essential, enabling examiners to closely check out welds for surface area problems such as cracks, porosity, and undercut. Calipers and fillet weld assesses are necessary for determining weld dimensions to verify compliance with style specifications.
Advanced devices prolong past visual aids, consisting of non-destructive testing (NDT) tools. Ultrasonic testing tools are essential in spotting subsurface flaws, using acoustic waves to expose internal stoppages without jeopardizing the weld's honesty. Likewise, radiographic screening utilizes X-rays or gamma rays to record images of a weld's inside, highlighting potential flaws.
Magnetic particle screening is an additional vital device, particularly for finding surface and near-surface interruptions in ferromagnetic materials. By applying ferrous bits and magnetic areas, inspectors can determine imperfections that might or else be unseen.
Dye penetrant evaluation is commonly used for non-ferrous materials, giving a contrast-enhanced visual look for surface-breaking issues. Welding Inspection Madison. Together, these devices enable welding examiners to adequately evaluate weld high quality, ensuring security and dependability in numerous applications throughout industries
Making Sure Architectural Integrity

Welding treatments need to adhere to established criteria and codes, such as those defined by the American Welding Society (AWS) or the International Company for Standardization (ISO) These standards guarantee that the welds can withstand environmental factors and functional tensions. Certified and accredited welders play an important role in this procedure, as their knowledge guarantees that strategies are applied correctly, lessening defects such as splits, porosity, and incomplete fusion.
Post-weld examination is one more essential element of verifying architectural stability. Non-destructive screening (NDT) techniques, consisting of ultrasonic screening and radiographic testing, are used to spot subsurface defects without endangering the welded structure. These examinations validate that the welds satisfy the called for quality requirements, giving guarantee of their sturdiness and integrity. view publisher site Ultimately, making sure architectural honesty in welding not only safeguards human lives however likewise shields investments and enhances the durability of crafted frameworks.
Conclusion
The fundamentals of welding inspection are important for maintaining the quality and safety and security of welded frameworks. By executing essential inspection methods, such as aesthetic evaluations and non-destructive testing, potential issues that can jeopardize structural honesty are recognized. Licensed inspectors are critical in ensuring conformity with market standards and reliable communication among stakeholders. Using specialized tools further boosts the evaluation process, inevitably securing human lives and prolonging the life-span of welded building and constructions.
Welding evaluation plays a crucial duty in guaranteeing the honesty, security, and long life of welded frameworks.Although welding inspection is important to guaranteeing the top quality and safety of bonded structures, it is the particular approaches employed that establish the effectiveness of the examination process. Secret welding assessment methods can be extensively categorized right into non-destructive screening (NDT) and destructive screening.Certified examiners play a critical function in the welding evaluation process, making certain that all welds comply with rigid sector standards and safety and security regulations.The basics of welding assessment are important for preserving the top quality and safety of welded structures.
Report this page